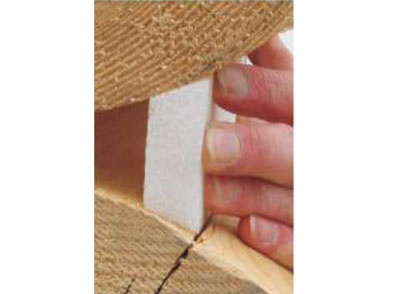
WHY USE BACKING MATERIALS
The fact is when applied to wood, any type of sealant, be it a high quality Perma-Chink Systems’ sealant, or a cheap construction caulk will perform better if a backing material is used in joints that are 1/4” or greater wide. The difference is that we want our customers to know the proper and best way to seal a joint so it does not fail, whereas most caulk manufactures don’t care. Their prime objective is to sell product and if repairs are frequently needed it means that they will potentially sell even more product.
The use of backing material behind a sealant serves two purposes; one, to assure the proper thickness of the sealant so that it can stretch and contract without breaking; and two, to provide a surface that the sealant will not bond to so that it can stretch without tearing away from the wood. The dynamics of sealing an exterior joint or crack in wood is the same regardless of the width of the gap or the product being used.
If the wood is unseasoned at the time a sealant is applied, the wood will shrink with time and in order to compensate for the shrinkage, the sealant must be applied in a manner that will allow it to stretch. When a sealant is applied too thick, once it cures it won’t be able to stretch enough to compensate for the wood’s shrinkage and may rip apart. When applied too thin it becomes too weak to stretch without breaking.
Think of it like a rubber band. A thick rubber band cannot stretch as far as a thin one. However if the rubber band is too thin, it will break when it is stretched. The same concept applies to sealants. If applied too thick, it can’t stretch without tearing and if too thin, it will be weak and will tear when pulled apart. In the case of sealants manufactured by Perma-Chink Systems, the magic number is an applied wet thickness of 3/8”. This results in a cured sealant with excellent elongation and maximum strength.
BACKING MATERIALS
Backing materials serve little purpose other than providing a suitable sealant thickness and surface for the proper application and performance of the sealant. A variety of materials can be successfully used. Some important features of a good backing material include:
- It must be inert and not outgas or react with the sealant.
- The sealant itself should not bond tightly to it.
- It should not wrinkle or deform when the sealant is applied over it.
- It needs to be able to withstand temperatures of at least 190ºF without warping or distorting.
There are a number of products specifically designed for use as backing materials for sealants. For smaller gaps, joints, and cracks, the most commonly used material is round backer rod. It comes in a range of sizes and is relatively inexpensive. Since it is flexible, it can be pushed into a crevice without needing to be nailed or stapled.
Grip Strip is designed for sealing larger gaps. Similar in composition to backer rod, it is shaped like a trapezoid so it can be squeezed in between round logs, although it can be used for a variety of situations. It provides a flat surface for chinking or sealing.
For wide chink joints between squared logs, we typically recommend the use of polyisocyanurate board (polyiso or R Max) or expanded polystyrene (EPS) beadboard. However, one side of the beadboard should be covered with a foil to help reflect the heat. If plain beadboard is used, you run the risk of the beadboard deforming on sunny areas where wall temperatures can reach over 180 degrees. When using foil covered beadboard, the chinking needs to be applied over the foil side.
Materials that should never be used as backing include Blueboard, or any other colored beadboard (they outgas and create blisters in the sealant), open cell foams (they absorb water), extruded polystyrene (causes blisters), Polyurethane foam (Pur Fill, Great Stuff, Styrofoam) or anything that you’re not sure about. If you are unsure or need some assistance with selecting the proper backing material to use for your job, give us a call and one of our technical people will give you an answer as to its appropriateness as a backing material.
What about joints that are too narrow to insert even the smallest diameter backer rod? In these situations a narrow strip of water-resistant masking tape works quite well. You don’t want to use masking tape that wrinkles when it gets wet since the wrinkles may show through the sealant. An excellent option is to use pinstripe tape, available at most automotive supply stores. The tape is vinyl, so it’s waterproof and our sealants won’t adhere to it. Pinstripe tape is available in widths down to 1/8”.
Leave a comment